Lean Methodology
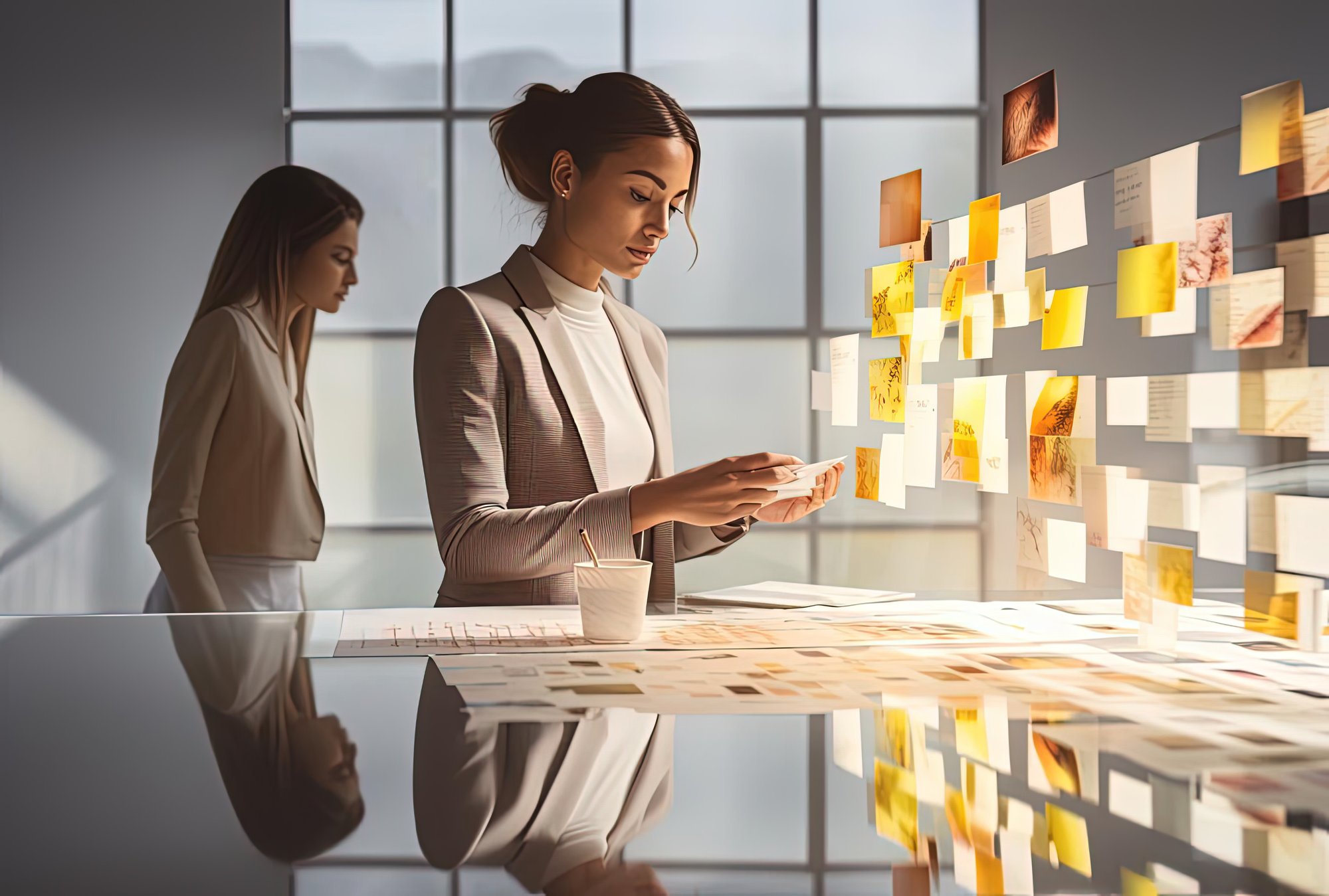
Lean Methodology
Lean methodology focuses on identifying and eliminating waste within processes. The idea is to streamline operations by removing unnecessary steps and optimizing resource usage. This way, every part of the process adds value to the customer, without wasting time, materials, or effort. It's a principle that originally grew out of Toyota's manufacturing process but has since spread across various industries worldwide.
Why Businesses Should Care About Lean Methodology
Adopting lean can transform a business, offering several compelling benefits:
Efficiency Boost
-
- By eliminating waste, businesses can do more with less, speeding up processes and reducing costs.
Improved Quality
-
- Lean emphasizes continuous improvement, which leads to enhancements in product quality and fewer defects.
Increased Customer Satisfaction
-
- When processes are lean, customers receive their products or services faster and with higher quality, leading to better customer satisfaction and loyalty.
Employee Engagement
-
- Lean encourages input from all team members, which can increase engagement and morale. Employees are more satisfied when they see their ideas contributing to improvements.
Flexibility and Agility
-
- Lean organizations can adapt more quickly to changes in the market or customer demands because they are less burdened by cumbersome processes.
How to Implement Lean Methodology
Implementing lean isn’t just a one-time project; it’s a cultural shift that requires ongoing commitment. Here’s how to get started:
Identify Value
-
- Begin by understanding what your customers value most about your products or services. This understanding will guide your decisions about what aspects of your process are essential and which are not.
Map the Value Stream
-
- Next, look at your entire process and map out the “value stream,” which is the sequence of activities required to design, produce, and deliver the final product or service to the customer. Identify any steps that do not add value and can be eliminated.
Create Flow
-
- After removing waste, reorganize the remaining steps to ensure smooth flow. The goal is to make sure the product or service is delivered to the customer without delays or bottlenecks.
Establish Pull
-
- Instead of pushing products through production based on predicted demand, use a pull system that responds to actual customer demand. This system reduces overproduction and inventory costs.
Pursue Perfection
-
- Lean is about continuous improvement. Regularly review and refine your processes to remove waste and improve quality.
Examples of Lean in Action
Manufacturing
-
- A car manufacturer might use lean to reduce inventory costs and production delays. This could involve reorganizing the assembly line to eliminate unnecessary movements or adopting just-in-time inventory to reduce excess stock.
Healthcare
-
- A hospital might implement lean to improve patient flow. By redesigning the process for admitting patients or scheduling surgeries, the hospital can reduce waiting times and improve patient care.
Software Development
-
- A tech company can apply lean principles by adopting agile methodologies, which focus on delivering value quickly and iteratively, responding to feedback, and continuously improving.
When to Use Lean Methodology
There is Significant Waste
-
- If a business process is bogged down by inefficiencies, delays, or high costs, lean can help streamline these processes.
Continuous Improvement Culture
-
- Lean thrives in environments where continuous improvement is valued. If your business encourages employees to find better ways to work, lean provides a structured approach to achieving this goal through the concept of "kaizen," or constant improvement.
Need for improvement
-
- If customer complaints are common due to product defects or service failures, lean can help identify the root causes and improve the process.
Customer-Focused Businesses
-
- Lean is centered on creating value for the customer. If your business prioritizes customer satisfaction, lean can help ensure that processes are aligned with customer needs, leading to higher satisfaction and loyalty.
Cost Reduction Goals
-
- If you're looking to reduce costs, lean can be an effective strategy. By identifying and eliminating waste, businesses can achieve significant cost savings while maintaining or improving quality.
When Not to Use Lean Methodology
Highly Creative or Innovative Work
-
- Lean's focus on efficiency may not align with highly creative or innovative tasks that require experimentation and flexibility. If your business relies on experimentation and flexibility, a more flexible approach like Agile might be more appropriate.
Rapidly Changing Processes
-
- Lean relies on standardized processes, which may not be suitable for businesses that experience constant changes in their operations. In such cases, a more adaptable methodology might be a better fit.
High Levels of Bureaucracy
-
- If your organization has a high level of bureaucracy, implementing lean might be challenging. Lean relies on quick decision-making and employee involvement, which can be hindered by excessive bureaucracy.
Stable, Low-Change Environments
-
- In industries where the processes and customer demands are very stable and predictable, the extensive effort to implement lean might not yield significant additional benefits.